Search
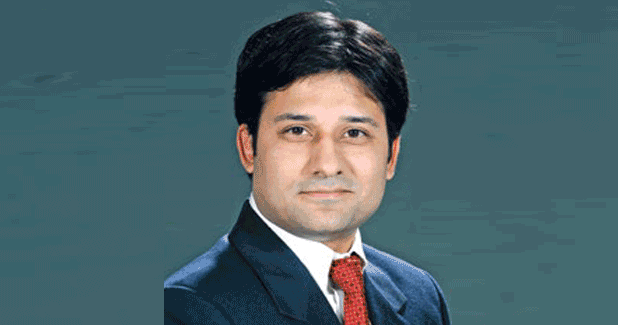
We emphasise on continuous product development
CASE India has maintained a leadership position in the Indian subcontinent riding on extraordinary customer connect and support. With the existing products like skid steer loaders, motor grader, compactor, loader backhoes etc, CASE India develops products to suit the evolving requirements of the Indian customers.
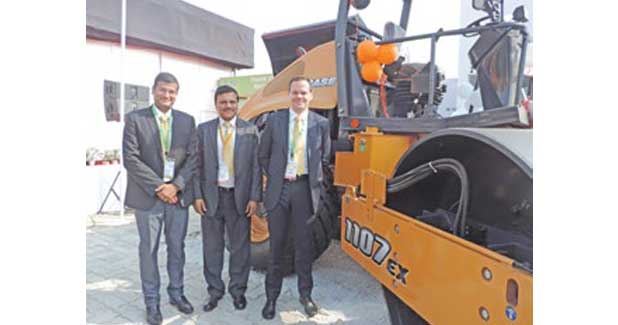
We continue to introduce technologically advanced products in India, which promises great opportunity and significant growth in 2017
We are launching globally renowned CASE Crawler Dozers in India with three new models ? 1150L, 1650L and 2050M in the 13 T, 18 T and 20 T operating weight range powered with FPT Industrial engine, significant for the roads and mining sector.
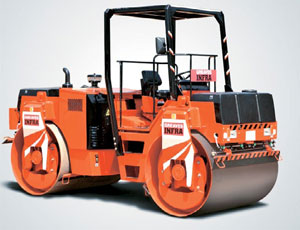
The growth of road equipment segment will be about 15 per cent by 2017
Last year, we took an aggressive approach with the launching of new products in spite of the recession. The objective was to be prepared and match customer expectations and take a chunk of market share when the economy turns around, says R Nandagopal, Chief Executive Officer, Construction Equipment Business, Greaves Cotton. Excerpts of the interview.
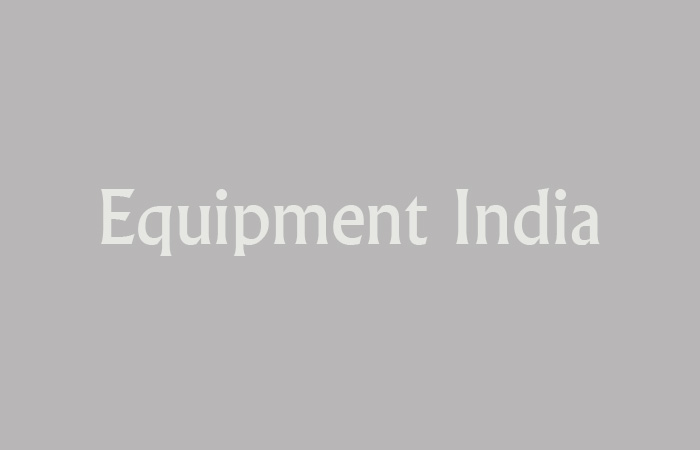
CASE showcases new machines
CASE Construction Equipment India displayed its recently launched EX` Series backhoe loaders and 1107 DX compactor at the 74th session of Indian Road Congress (IRC). The event provides a national forum for sharing of knowledge and pooling of experience on the construction and maintenance of roads and bridges, including technology, equipment, research, planning, finance, taxation, organisation and related policy issues. This year's edition was held in Guwahati from 18 to 22 January 2014.
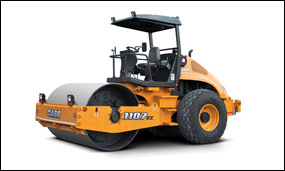
New CASE Vibratory Soil Compactor
CASE Construction Equipment launched a new 1107 DX vibratory soil compactor which completes the compactor line-up alongside the upgraded 752 and the smaller 450 DX.The new 1107 DX completes CASE -?s compactor offering, which also includes the 450 DX and the 752 at the lower end of the range that puts CASE in the lead of this segments market. The new model takes operator comfort and safety to new levels, while delivering a reliable performance with excellent fuel efficiency.
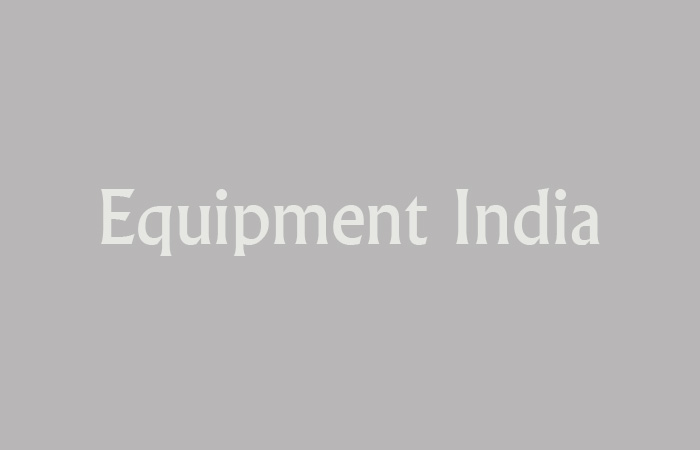
Building the Best Roads
Volvo machines, with their fuel efficiency and robustness, stand out amongst all the others.For all that eastern shoulder of India has an untouched, mesmerising beauty, most of eastern Assam did not have good roads until a few years ago. However, once the roads were in place, there was no turning back.
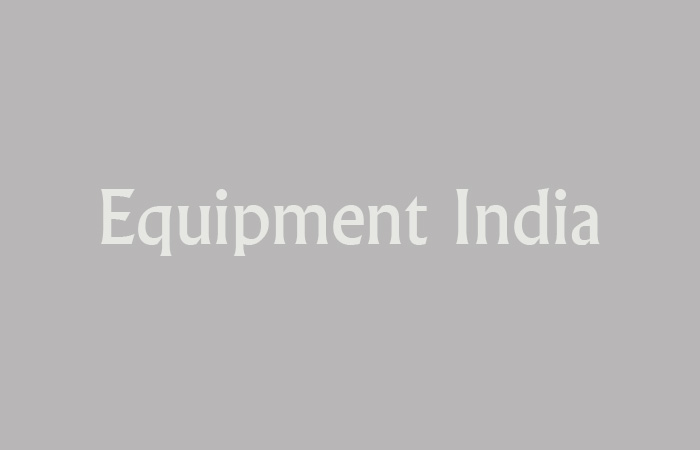
JCB manufactures products which are robust, custom built and highly fuel-efficient.
JCB offers a world class vibratory soil compactor VM115 and a recently launched 9 T Tandem Roller VMT 860, which are specifically used for road projects. These machines are built specially for Indian roads and are amongst the best at compaction, says Amit Gossain, VP - Marketing & Business Development, JCB India. Excerpts from the interview.
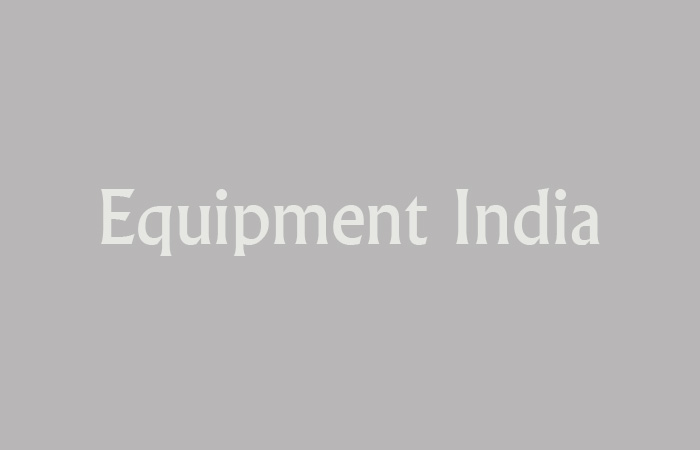
Compacting Technology Set to Improve
The new trend in technology is faster compaction by achieving the required density at a lower operating cost. Also, the latest equipment is designed with features to improve operator safety, comfort and maintainability.
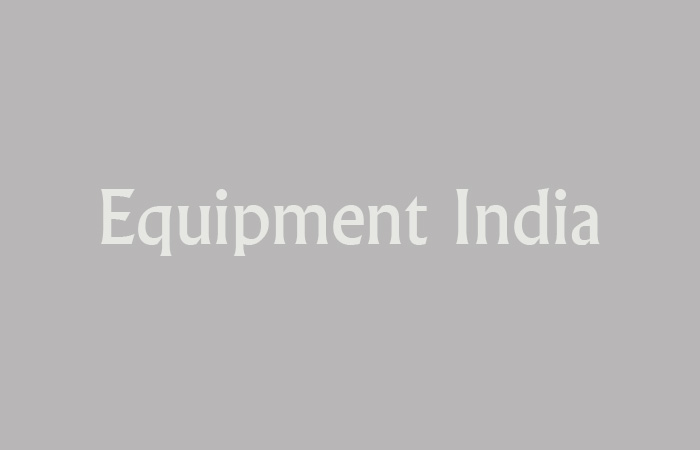
Cat at the Heart of Gammon Projects
With a fleet of more than 80 Cat machines, Gammon banks on Caterpillar for smooth sailing, peak performance levels and timely completion of its infrastructure projects.
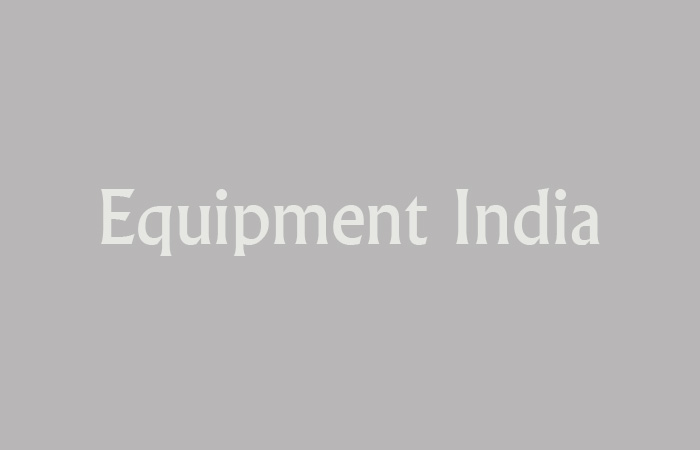
Caterpillar has vibratory soil compactors in the operating weight range of 4.5T?18.5T
The popular model being offered in India is the CS533E (11T Class) which is required to meet the National Highway Project requirements in India,? says Pankaj Dara, Associate Vice President - Construction, TIPL. 0 - - 15633 14 102 2011-05-02 00:00:00.000 Equipment India Hamm is the technology leader in compaction equipment
?Our existing manufacturing facility can produce 400 machines annually and plans are on for further expansion in the coming years,? says Girish Dixit, Head - Engineering & Design, Wirtgen India. In a freewheeling chat, Girish speaks about the industry trends.
Tell us about the range offered in compaction equipment and also their unique features?
Wirtgen India offers Hamm-11T soil compactor, 9T asphalt compactors and 24T pneumatic tyre rollers (PTR) for the Indian market. Hamm compactors come with German design and technology mainly featuring excellent operator comfort and safety. The equipment are powered by a fuel-efficient and highly durable water-cooled engine.
Hamm is the technology leader in compaction which has been awarded many design prizes for its latest innovations. Recently, it was awarded iF-Gold award 2010 also called the Design Oscar for new HD+ series of asphalt compactor. The GRW 280, rubber-wheeled rollers received the iF Design award 2010.
Higher quality level of the components used in Hamm compactors increases the durability of the equipment. Better serviceability and reduced maintenance frequency with less fuel consumption results in the lower operating cost of the equipment.
What is the existing manufacturing capacity for these product lines?
Our existing manufacturing facility can produce 400 machines annually and plans are on for further expansion in the coming years.
What is the rental scenario for these products?
Currently, Wirtgen India is not in the rental market and is only selling the new equipment in the retail and corporate segments, rental companies.
Are these products compliant with the Bharat stage III emission norms?
Yes, the equipment built after April 2011 will comply with Bharat stage III emission norms.
How do you look at the replacement/ repowering market for the units sold which are not complying with Bharat stage III norms?
As per the regulations, no replacement/re-powering is required for the units built with Bharat stage II norms.
Why vibratory compactors over static ones and what is the vibration effect in compaction over the static loading?
Vibratory compactors develop dynamic force in addition to the static load and total applied force is the sum of dynamic force and the static weight of the machine. For example, Hamm 11T soil compactor generates 24T dynamic force and with 6.8T static weight at the drum will induce 30.8 tonne load on the ground. The advantage of using 11T vibratory soil compactor versus 30 tonne static compactor is evident from this.
The vibratory compactor with drum vibrating at higher amplitude will result in compacting the higher lift thickness and achieving the required density compared with the static roller. In the static roller, the linear load is not uniform over the width of the machine (one front roller and two rear rollers) which results in uneven mat finish. In the vibratory compactors, the linear load is uniform along the width of the drum.
To what extent do soil conditions determine the selection of compactors? Could you tell us the reasons?
Type of soil and conditions like moisture content decides the achievable density within the required number of passes. It is important to select the suitable compactor which will develop the required force to achieve the density with lesser number of passes on the appropriate lift thickness.
What determines the maximum achievable density?
Density depends on the soil characteristics (type of soil) and optimum moisture content (OMC) present in the soil. Generally, 95 to 100 per cent density can be achieved with 11T soil compactors on the appropriate lift thickness.
?To have maximum return on investment, the equipment should have maximum productivity and less rework,? says SM Roy, Chief Executive Officer, Lanco Infratech. In an exclusive chat with Equipment India, Roy elaborates on the evolution of compacting and grading technologies. Excerpts from the interview.
How, over a period, have the methods of compaction and grading evolved and to what extent does the contracting fraternity use the advanced equipment and methodology?
The first road roller was horse-drawn; this was followed by steam and diesel rollers. For a long period, static compactors of various sizes were used. The introduction of vibratory compactor in 1946 opened a new era in construction industry.
A few decades ago, grading was done manually or with tractor dozers where operator skill was important for accuracy. Advanced technology has made the grading work simple by giving option of automatic slope and elevation offsets. GPS navigation and machine guidance systems have reduced the amount of external surveying required.
Almost every construction project or site preparation requires some kind of grading and compaction. The Indian contracting community extensively uses the graders and compactors for various purposes based on size and extent of projects.
Why vibratory compactors over static ones? What is the vibration effect in compaction over static loading?
Static compactor functions with its own weight and hence compaction is confined to the top soil layer. Vibratory compactors use a mechanism to create a downward force in addition to the machine's static weight thereby affecting the top layers as well as deeper layers. Vibration moves through the material, setting particles in motion and moving them closer together for the highest possible density.
To what extent does the soil condition determine the selection of compactors?
The desired level of compaction is best achieved by matching the soil type with its proper compaction method. Clay is cohesive; its particles stick together requiring high impact force to compact. Hence, the sheep-foot roller is the best choice. Best compaction of granular soils is possible with shaking or vibratory action. For mixed type of soils, it is a good idea to choose the compactor appropriate for a larger percentage of the mixture.
What is the return on investment on a compactor and on a grader?
To have maximum return on investment, equipment should have maximum productivity and less rework. Production cost depends on depreciation, maintenance, fuel, working hours and labour. Smaller machines cost less in terms of ownership but more in labour and vice versa. In general, for each situation, one should study equipment productivity and try to strike a balance to get better value for money.
Could you tell us about the density achievable from the range of compactors? What determines the maximum achievable density?
The maximum achievable density depends on fill type, compactive efforts and moisture content and it varies from 2.1 tonne/cu m for well graded gravels to 1.5 tonne/cu m for highly plastic clays. Most of the compactors can achieve maximum fill density with different compactive efforts and efficiencies.
What are the variants in compaction?
The variants in compaction are soil type, moisture content, lift or fill thickness, compactive efforts or number of passes of compactors.
Selection Criteria:
A selection criterion for graders and compactors is given below:
? Size, weight and machine power.
? Steering, direction control and maneuverability.
? Functional automation.
? Multi-tasking machine with various attachments.
? Maximum possible thickness of the lift (for grader).
? Accuracy of the grading (for grader).
? Range of vibration frequency (for compactor).
? Working and downtime.
? Ownership and maintenance cost.
? Availability of trained manpower to use the machine.
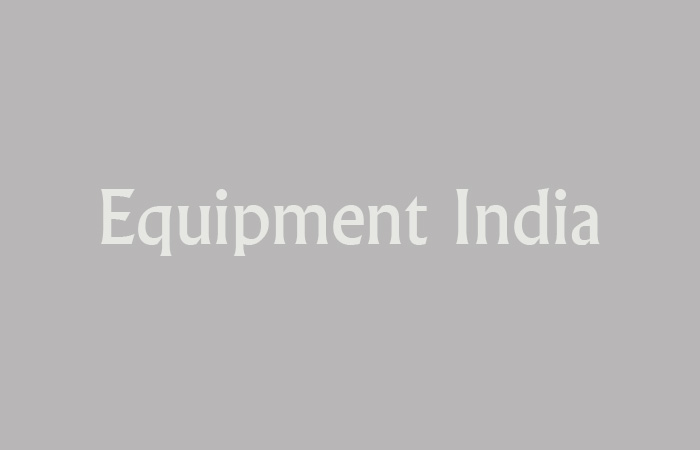
Volvo is first OEM to announce the launch of telematics system
?The market volume for excavators is expected to be around 7,000 machines and this is expected to touch 15,000 in the next five years, says AM Muralidharan, Managing Director, Volvo India.
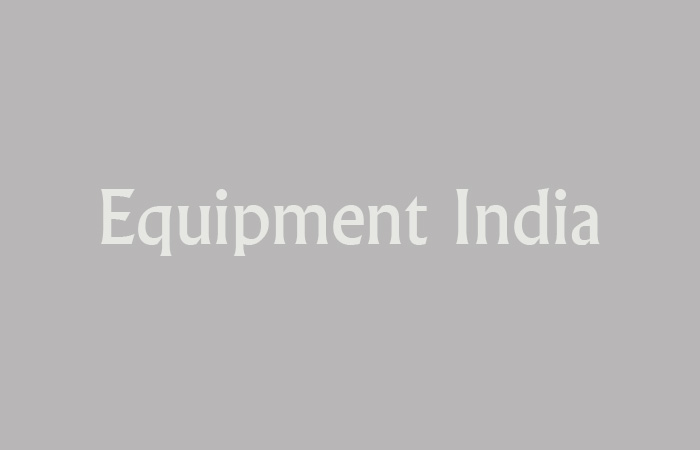
The Rental Center is dealer for LiuGong
LiuGong Construction Machinery, has appointed The Rental Center of Monticello in the state of New York, as a dealer.